The rotating mechanism 1


The rotating mechanism 1

The rotating mechanism 2

The rotating mechanism 3

The dockside gantry crane
The dockside gantry crane
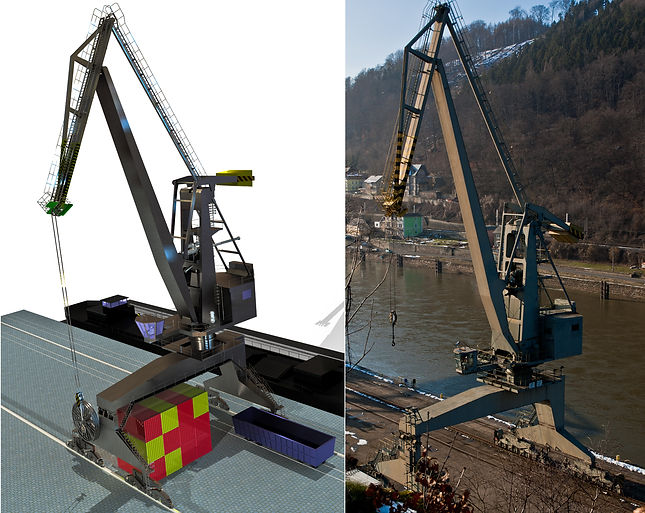
Equipment of the crane
The rotating mechanism
The tilting mechanism
The telescopic mechanism


The telescopic mechanism

The tilting mechanism
This model simulate basic movements during Work in port. It includes rotation of upper tower on huge bearing, Which is driven by two pinions.
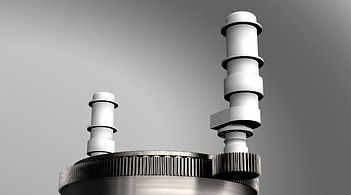
-
Large-sized bearing. (Axial, roller)
-
Crown gear.
-
Two driving pinions.
-
Electric motor with a four-speed gearbox
-
Hydraulic control.
-
Ejecting of rollers using hydraulic fluid.
-
Subsequent boom extensions.
-
The entire device is tilted.
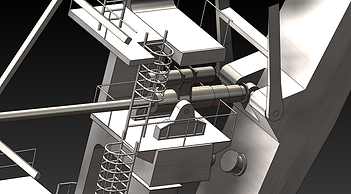
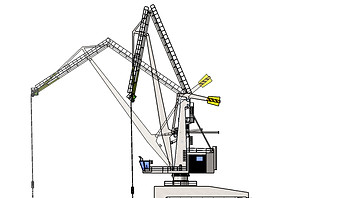
The rotating mechanism
The telescopic mechanism
Tilting of the crane's boom
The movable counterweight
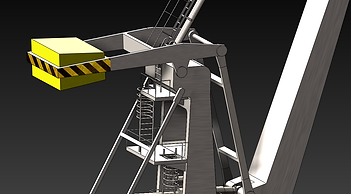
-
Mounted to the main tower and beam type, which is mounted on the main beam.
-
When the boom tilt, the counterweight moves upward.
-
Ensures constant crane capacity.
-
Weights 22.5 tons.
The movable counterweight
The movable counterweight


The movable counterweight
This is my final work at technical secondary school in 2013. The goal was creating complete moveable crane. I was able to create model by using SolidWorks. As my pattern, I chose dockside gantry crane located in port of Decin upon river Elbe. I cooperated with local manager, who provided drawings for me.
The whole final work lasted over 3 months. It helped me to develop my skills in SW modeling, rendering and creating animations.
After completion of the final work I had to present it before graduation committee and I was successful.
Also with this final work, I competed at the national round of Students` Professional Activities in Brno. It was my first opportunity to present myself and my work to a jury and an audience.

Description
-
Gantry crane with a jointed booms.
-
Used for loading lump materials.
-
Highly movable.
-
High lifting speeds and driving.
-
Large operational range with short handling times.
-
Travels on rails.
-
The upper construction is rotatable by 360 degrees.
-
Joint construction mounted with a movable counterweight.
-
Due to the movement of the counterweight is a constant load capacity.
-
For tilting of the boom uses hydraulic mechanism.
Comparison of reality and the model.
Rocker Mechanism
The telescopic mechanism
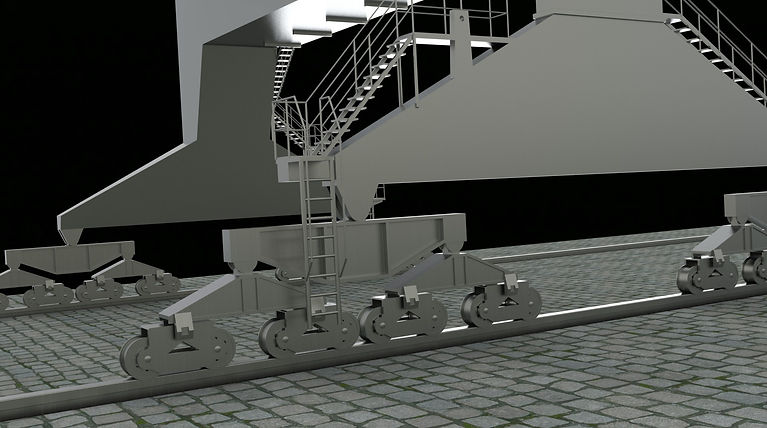
-
The rockers spread the weight evenly on all casters.
-
Able to carry up to several dozents tonnes.
-
Better stability and the contact surface.
-
The steel construction must be able to carry tens of tons.
-
One massive steel welded box beam.
-
Equipped with a joint (deflection, dilatation).
-
High rigidity.
-
Heavier construction = large load on embankment

Construction of the portal
-
Placed on top of the rotary construction.
-
Adequate view of the service area, overlooking the ship.
-
Control of drive, rotation, tilting the boom and coiling the rope.

The control cab





